The Scientific Research Behind Porosity: A Comprehensive Guide for Welders and Fabricators
Understanding the intricate devices behind porosity in welding is vital for welders and producers striving for impeccable workmanship. From the structure of the base materials to the intricacies of the welding procedure itself, a wide range of variables conspire to either exacerbate or relieve the visibility of porosity.
Comprehending Porosity in Welding
FIRST SENTENCE:
Exam of porosity in welding exposes critical insights right into the integrity and high quality of the weld joint. Porosity, identified by the presence of tooth cavities or spaces within the weld metal, is an usual concern in welding processes. These gaps, otherwise properly dealt with, can compromise the structural honesty and mechanical buildings of the weld, bring about prospective failings in the ended up item.

To identify and evaluate porosity, non-destructive testing approaches such as ultrasonic screening or X-ray assessment are commonly utilized. These methods enable for the identification of inner issues without jeopardizing the integrity of the weld. By analyzing the dimension, form, and distribution of porosity within a weld, welders can make informed choices to enhance their welding procedures and accomplish sounder weld joints.
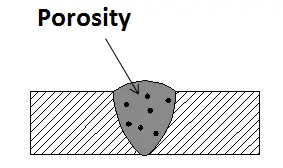
Aspects Influencing Porosity Development
The incident of porosity in welding is influenced by a myriad of elements, ranging from gas protecting efficiency to the complexities of welding specification settings. Welding specifications, including voltage, current, travel speed, and electrode kind, additionally influence porosity development. The welding method utilized, such as gas metal arc welding (GMAW) or shielded metal arc welding (SMAW), can affect porosity development due to variants in heat distribution and gas coverage - What is Porosity.
Results of Porosity on Weld Top Quality
The visibility of porosity additionally compromises the weld's resistance to rust, as the entraped air or gases within the voids can react with the surrounding atmosphere, leading to destruction over time. Additionally, porosity can hinder the weld's capacity to withstand pressure or effect, additional threatening the total quality and reliability look what i found of the welded structure. In vital applications such as aerospace, auto, or architectural building and constructions, where safety and resilience are critical, the damaging impacts of porosity on weld high quality can have serious repercussions, highlighting the significance of reducing porosity through proper welding techniques and procedures.
Strategies to Decrease Porosity
To boost the top quality of bonded joints and make sure architectural honesty, welders and makers utilize particular techniques targeted at reducing the development of spaces and tooth cavities within the material throughout the welding process. One effective approach to lessen porosity is to make sure proper product prep work. This includes comprehensive cleansing of the base steel to remove any type of contaminants such as oil, oil, or wetness that could add to porosity formation. In addition, using the appropriate welding criteria, such as the appropriate voltage, click here to find out more current, and take a trip speed, is crucial in protecting against porosity. Preserving a consistent arc size and angle during welding additionally helps in reducing the probability of porosity.

In addition, selecting the right protecting gas and maintaining correct gas circulation prices are important in decreasing porosity. Using the suitable welding strategy, such as back-stepping or employing a weaving movement, can additionally help distribute warm equally and decrease the possibilities of porosity formation. Guaranteeing correct ventilation in the welding atmosphere to get rid of any kind of prospective sources of contamination is vital for achieving porosity-free welds. By executing these techniques, welders can properly lessen porosity and create top quality bonded joints.
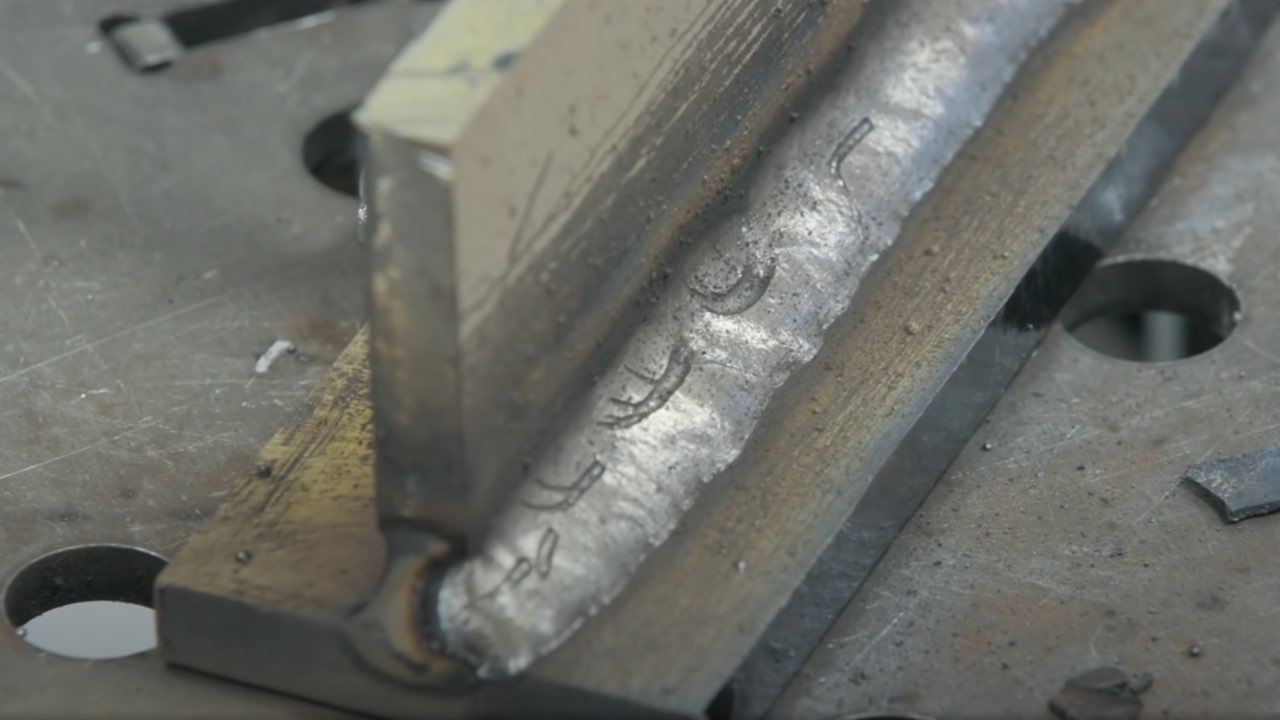
Advanced Solutions for Porosity Control
Implementing sophisticated innovations and innovative techniques plays an essential role in attaining remarkable control over porosity in welding processes. One sophisticated solution is the usage of advanced gas combinations. Protecting gases like helium or a mixture of argon and hydrogen can help in reducing porosity by offering far better arc stability and boosted gas coverage. Furthermore, employing sophisticated welding strategies such as pulsed MIG welding or modified ambience welding can also assist mitigate porosity problems.
One more sophisticated solution involves using innovative welding equipment. Using devices with integrated features like waveform control and sophisticated power resources can boost weld quality and reduce porosity dangers. The execution of automated welding systems with exact control over specifications can dramatically reduce porosity issues.
In addition, incorporating innovative surveillance and examination innovations such as real-time X-ray imaging or automated ultrasonic screening can help in spotting porosity early in the welding procedure, enabling instant restorative activities. On the whole, incorporating these advanced remedies can considerably boost porosity click here for more control and enhance the overall top quality of bonded parts.
Verdict
In conclusion, understanding the scientific research behind porosity in welding is vital for welders and producers to produce high-grade welds - What is Porosity. Advanced remedies for porosity control can additionally enhance the welding process and guarantee a solid and reliable weld.
Comments on “Comprehensive Guide: What is Porosity in Welding and Exactly How to stop It”